Gantry CNC machining centers are pivotal in the world of precision machining, catering to a wide array of industries and applications. These versatile machines are known for their gantry structure, which consists of two vertical columns supporting a horizontal crossbeam. The spindle and tooling are mounted on this crossbeam, while the workpiece is secured on the worktable below. In this article, we will explore various types of gantry CNC machining centers and their specific applications.
1. Vertical Gantry Machining Center
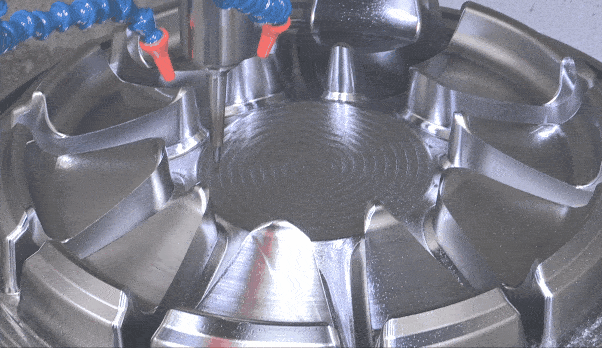
The vertical gantry machining center is characterized by its vertically oriented spindle. This configuration is ideal for milling, drilling, and boring operations on large or heavy workpieces. Industries such as aerospace and automotive manufacturing often rely on vertical gantry machines for their precision and versatility.
2. Horizontal Gantry Machining Center
In contrast, the horizontal gantry machining center features a horizontally oriented spindle and a horizontal worktable. This setup is suitable for milling and drilling operations on long and large workpieces, commonly used in applications like shipbuilding and steel processing.
3. 5-Axis Gantry Machining Center
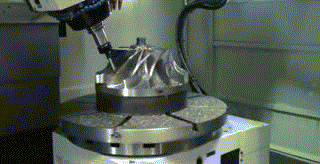
For complex and intricate components, the 5-axis gantry machining center is the go-to choice. With the ability to move the cutting tool in five axes, including X, Y, Z, and two additional rotational axes, these machines offer superior flexibility and precision. They are essential in industries that demand highly contoured and detailed parts, such as aerospace and medical device manufacturing.
4. Bridge-Type Gantry Machining Center
Bridge-type gantry machines are recognized for their two-column support at one end of the machine, leaving the other end open for easy workpiece loading and unloading. They are often used in industries requiring the machining of large and heavy workpieces, such as mold and die making.
5. Cantilever-Type Gantry Machining Center
In the cantilever-style gantry machining center, one column supports the gantry structure, which extends outward. This design is preferred when access to the workpiece is crucial and is used for machining large, irregularly shaped components.
6. Traveling Column Gantry Machining Center
Traveling column gantry machines feature a fixed gantry structure while the worktable moves along the longitudinal axis (X-axis). They are suitable for applications where workpiece stability and precision are of utmost importance.
7. Double Column Gantry Machining Center
Double column gantry machines are designed for heavy-duty machining tasks. With two vertical columns on either side of the worktable, they offer excellent stability and precision. These machines are frequently employed in applications such as large mold and die manufacturing, as well as components used in the automotive and aerospace industries.
8. High-Speed Gantry Machining Center

High-speed gantry machining centers are tailored for fast and accurate machining of light to medium-sized components. They find application in industries where rapid cutting and high precision are required, such as aerospace, electronics, and mold making.
9. Multi-Spindle Gantry Machining Center
Multi-spindle gantry machines are equipped with multiple spindles, allowing for several operations to be performed simultaneously on a workpiece. These machines are ideal for increasing productivity in high-volume manufacturing settings.
In conclusion, gantry CNC machining centers come in various types and configurations, each suited to different industries and applications. Choosing the right type of gantry machine depends on factors such as the size and complexity of the workpiece, the material to be machined, and the desired production output. With these versatile machines at your disposal, you can achieve high precision and efficiency in your machining operations.