CNC machining centers have become the equipment of choice for many businesses seeking efficiency and quality due to their high accuracy, efficiency, and versatility. However, due to the existence of different types of machining centers in the market, choosing the right machine may be a bit difficult for those unaware of these different types. Next, LEWE will introduce the classification of machining centers and their application areas in detail, to help people better choose and use machining center equipment.
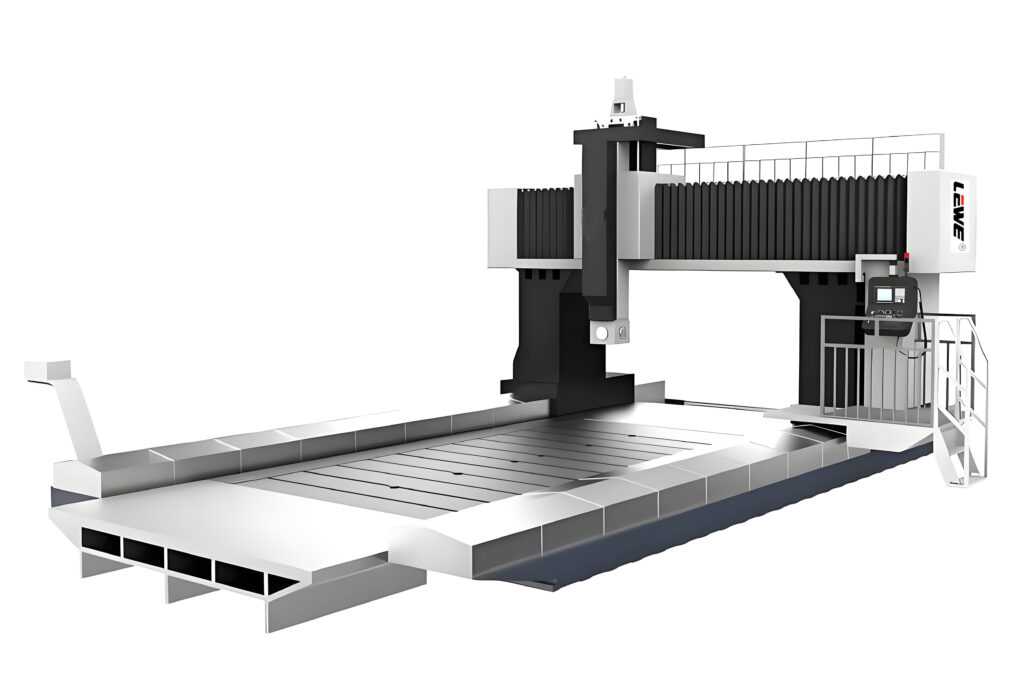
Firstly, Classification according to the type of processing
- CNC milling machining center: mainly used for milling processing, with high processing accuracy and processing efficiency, commonly used in complex parts and high-precision parts processing.
- CNC turning machining center: mainly used for turning to process, can achieve turning, milling, drilling, and other processing operations, commonly used in shaft parts and disc parts processing.
- CNC grinding machining center: mainly used for grinding processing, with high-precision grinding capacity and processing efficiency, commonly used in ultra-precision parts and high-hardness parts processing.
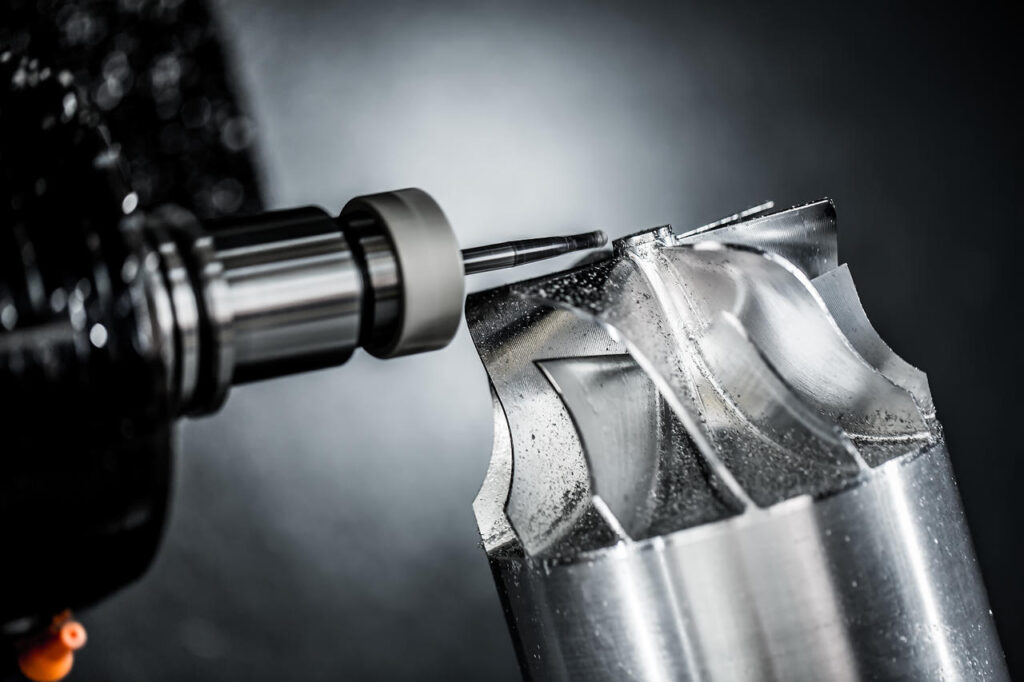
Secondly, Classification according to the number of control axes
- Tthree-axis CNC machining center: only with three linear axes, can achieve any point in the plane of the processing, commonly used in small and medium-sized parts processing.
- Five-axis CNC machining centers: with three linear axes and one or two rotary axes, can achieve the processing of complex parts, especially for the processing of space surfaces and inclined surfaces.
- Multi-axis CNC machining center: with more than three linear axes and more than two rotary axes, can achieve any space surface processing, commonly used in large and complex parts processing.
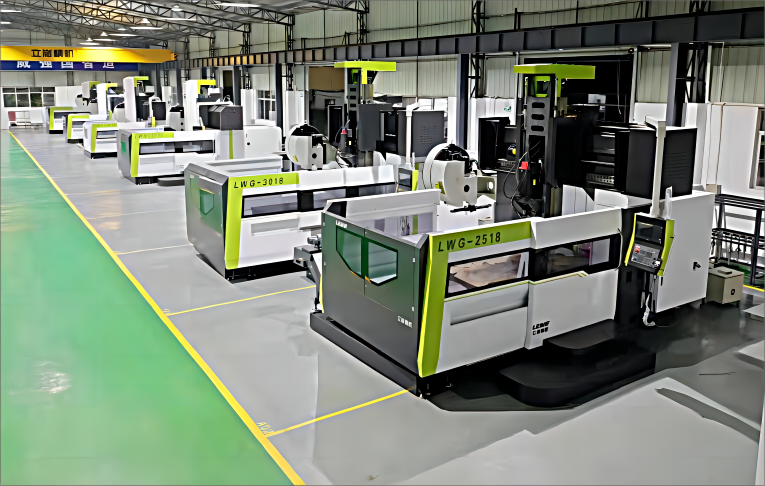
Thirdly, Classification according to layout
- Vertical CNC machining center: the spindle is perpendicular to the worktable, covering a small area, compact structure, suitable for small parts processing.
- Horizontal CNC machining center: the spindle is parallel to the table, suitable for large parts machining.
- Gantry CNC machining center: the spindle is located in the gantry, with a large machining range and rigidity, suitable for large and heavy parts processing.\
- Composite CNC machining center: simultaneously with vertical, horizontal, and other layout forms, can
Finally, Classification according to the accuracy level
- Ordinary CNC machining centers: the accuracy level is generally ±0.01mm, applicable to general precision machining needs.
- High-precision CNC machining centers: the accuracy level is generally ± 0.005mm or higher, applicable to high-precision, high-demand processing needs, such as aerospace, precision instruments, and other fields.
- Ultra-high-precision CNC machining centers: the accuracy level is generally ± 0.001mm or higher, applicable to the processing of ultra-precision parts, such as clocks and watches, optical instruments, and other fields.
In short, there are more ways to classify CNC machining centers, and different types of CNC machining centers have different characteristics and application scenarios. When choosing a CNC machining center, you need to make comprehensive consideration according to the actual processing needs and production conditions and choose the most suitable type of CNC machining center to improve processing efficiency and processing quality.